Verlumina
A lamp shade crafted from a renewable
biomass source, showcasing the beautiful
potential of sustainable bioplastics.
Bioplastic Formula
Material Research
After numerous experiments with varying ratios of the ingredients were conducted, and a mixed gel of both agar and gelatin was found to have the best properties.
Experimental Molding Process
Learning to work with an unpredictable material and control its form.
DRAPE MOLDING
A flat sheet of bioplastic can be poured, left to partially dry, then draped into a mold. Similar to draping fabric, only simple curves can be accomplished.
PROCESS
Once draped, the material is buried in silica gel to rapidly dry the bioplastic and prevent mold growth
STRETCHING
Like leather, the bioplastic can also be stretched around corners to form more exacting geometry.
Clips used to tightly hold stretched material
The bioplastic shrinks around the mold as it dries, forcing it to take on the mold’s exact geometry
DESIGN EXPLORATION
Inspired by the translucence of the material, I decided to design a lamp that would showcase the material’s beauty. Modules make up a dodecahedron that acts as a shade for a light.
Modules take advantage of the regular geometry accomplished when stretching the material, while also embracing the material’s natural tendency to drape and curl.
Each module is repeatable, yet entirely unique
COLORANT FROM LOCAL GRASS
GRASS CLIPPINGS : A WASTED RESOURCE
90 million gallons of water are used for growing grass for an average golf course in California, which is the highest nonagricultural use of water in the state. Furthermore, grass clippings are wasted and take up a large amount of space in composting sites and landfills.



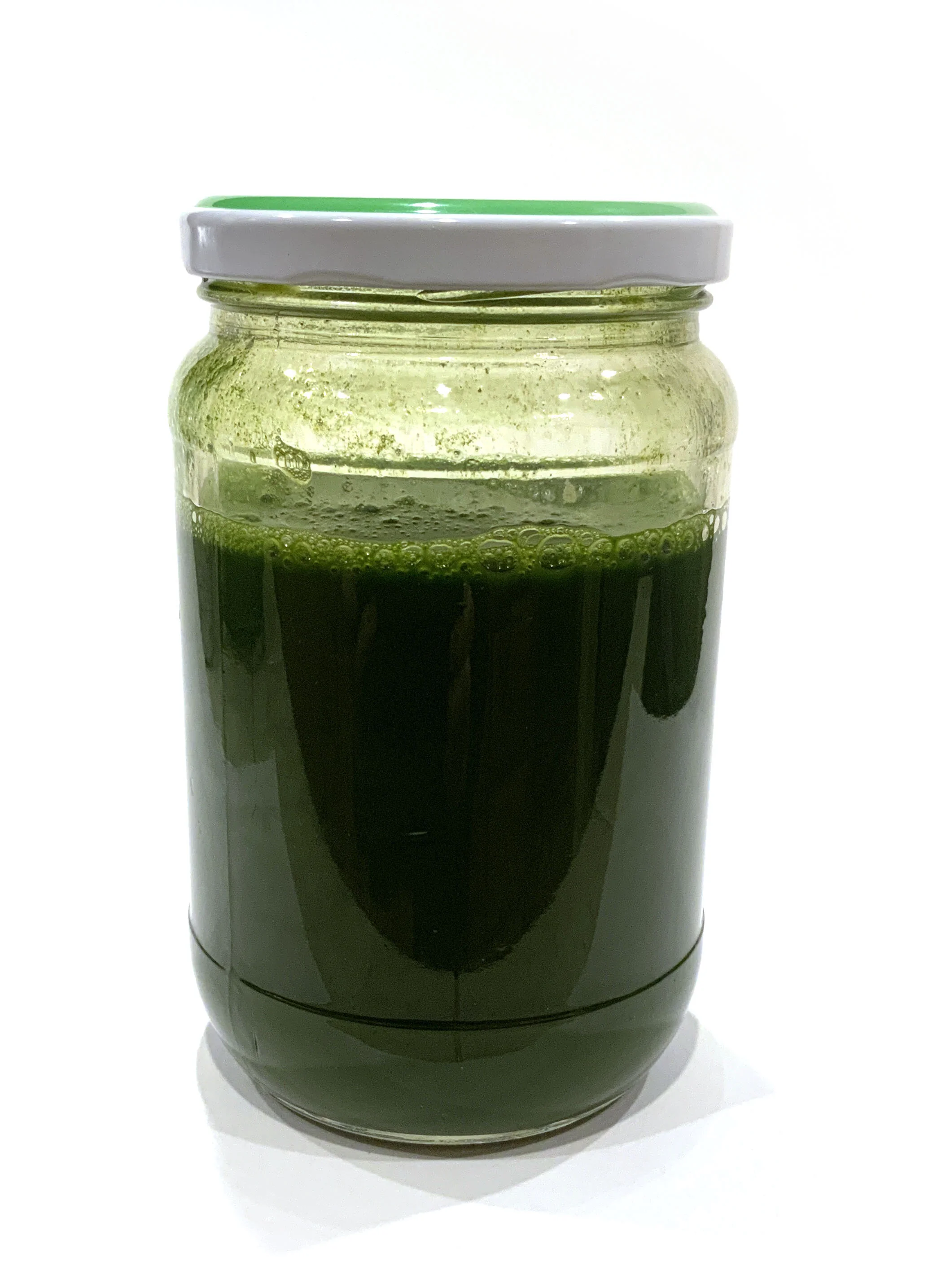

MOLD DESIGN
The reusable core and cavity of the mold were designed and 3D printed to form the bioplastic into a repeatable module.
The open frame allowed silica gel to quickly dry the bioplastic.
FIRST ITERATION
Material not able to drape naturally
Outer ring did not clamp material well
SECOND ITERATION
Bioplastic onstrained by walls, similar to original drape molding method
Shrinks around inner ring, creating sharper repeatable geometry at the base
PRODUCTION PROCESS
12 modules created in total
Cycle time (from pouring to dry product): ~ 36 hours
Modules held together with copper wire in corners
Each module consists of:
2g agar agar
15g gelatin
3.75g glycerol
75g distilled water
18g grass pigment
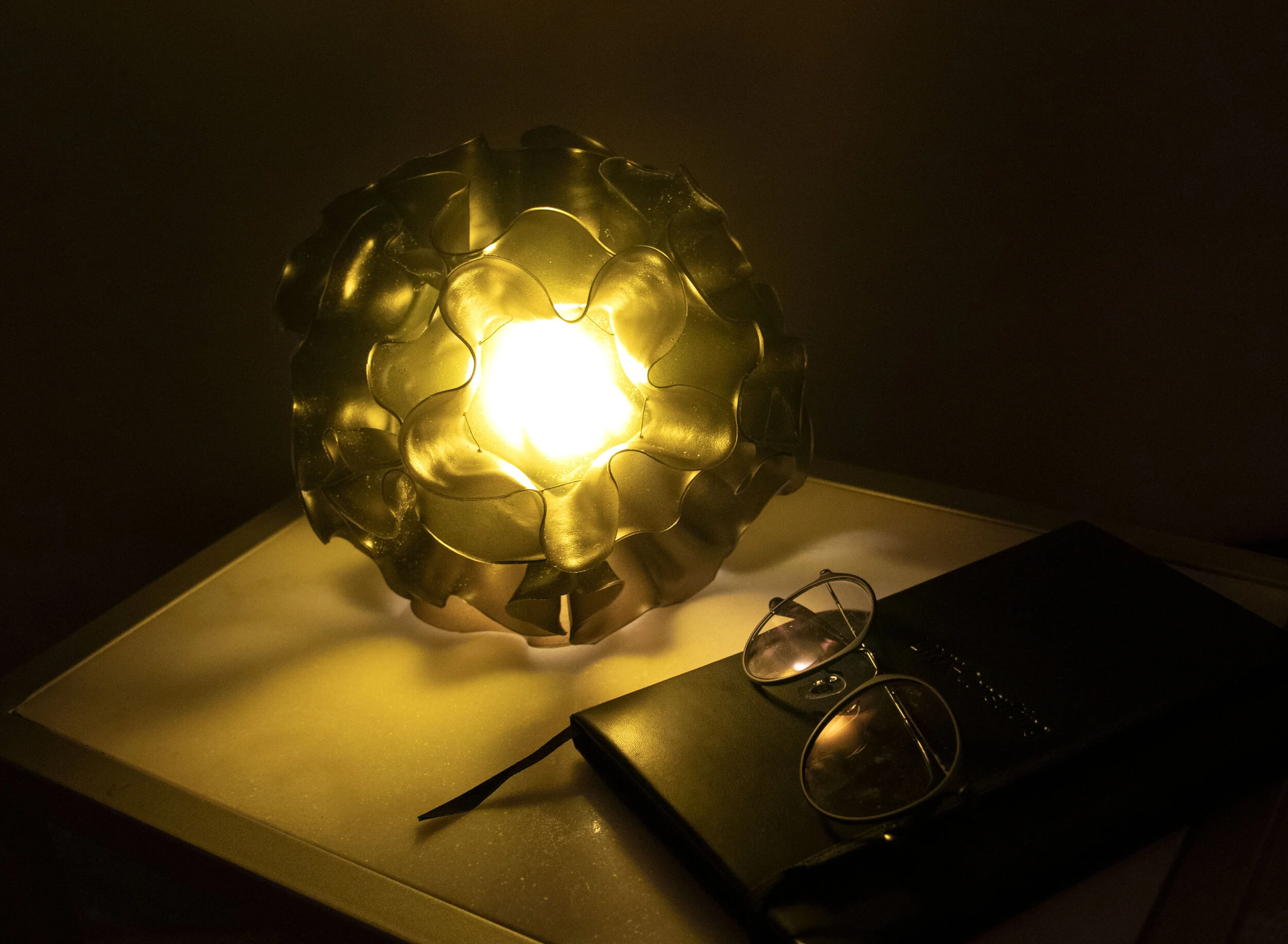